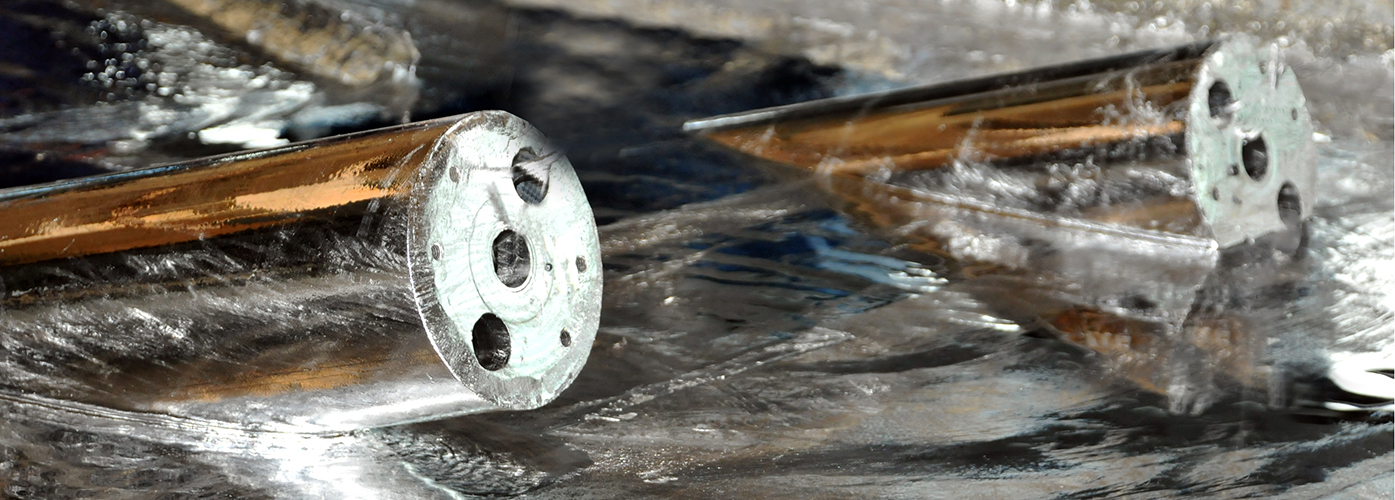
Hot-dip Galvanizing service
General information
In the hot-dip galvanizing shop, the equipment of the German company “Pilling”, “SCHEFFER”, “Stoeckl”, the Austrian company “KOERNER”, “SCHEUCH” and the Norwegian company “C.H.Evensen” was installed.
The application of the experience of Western European countries made it possible to create the most advanced and environmentally friendly Plant for the production of anticorrosive coatings in the region. This enterprise has a large production capacity.
In the hot-dip galvanizing shop, the equipment of the German company “Pilling”, “SCHEFFER”, “Stoeckl”, the Austrian company “KOERNER”, “SCHEUCH” and the Norwegian company “C.H.Evensen” was installed. The annual production capacity of the plant is 20,000 tons. Metal constructions with dimensions up to 14,5x1,4x2,7 meters can be galvanized here in automatic mode. It is also possible to galvanize structures with a length of up to 18 meters in manual mode.
Primary treatment of metal is carried out with the use of 9 (nine) technological baths placed in a compacted area, of a dryer capable of drying 3 (three) cross-beams at a time, and of a gas scrubber intended for the capture of HCl fumes (hydrochloric acid fumes) in the air of the area where the baths are placed.
Monitoring of zinc coat is carried out by testing methods corresponding to GOST 9.307-89 state standard. The metal composition of the zinc bath is analized with the use of BELEC LAB 3000s stationary spectrometer. Technical lifetime of galvanized materials equals to 75-100 years. Galvanized materials are widely used in different spheres where reliability and durability are demanded.
Flux layer acts as a catalyst during galvanization process. It also blocks the possible generation of oxides in the drying chamber or during the transportation of cross-beams to the zinc bath. The drying process is carried out in heated air with the use of a 110-120°C warm-air furnace.
During hot-dip galvanizing metal constructions get submerged into a bath filled with molten zinc (~450-452°C). Galvanized materials meet the requirements of EN ISO 1461:2009, ASTM A123 standards. In order to ensure the high quality of galvanization process a high-purity (99.995%) zinc is used.