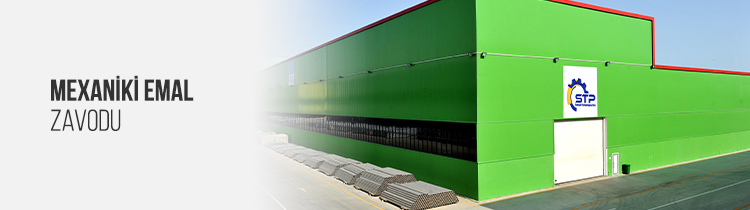
Mechanical processing plant
General information
With a view to reviving the nation’s machine-building and metalworking industry and increasing interest on the domestic market, the Mechanical Processing Plant was built and commissioned into operation as part of the Sumgait Technologies Park (STP).
With a view to reviving the nation’s machine-building and metalworking industry and increasing interest on the domestic market, the Mechanical Processing Plant was built and commissioned into operation as part of the Sumgait Technologies Park (STP). The plant has the most advanced equipment and mechanisms for the production of metal semi-finished products, precision processing, machining, press-workshops and heat treatment.
The Precision Machining Shop is a unique enterprise in the region that was created for the CNC-based production of machine components and complex mechanisms. Covering a total area of 13,584 m² and housing 41 Mazak machines, the workshop provides for the production of metal products requiring high-precision machining.
Some of the processes carried out here include the precision machining of machine parts and production of parts of turbine equipment, and the error ratios in these products are measured by microns. The annual production capacity of the precision machining shop depends on the dimensions and material of the ordered parts.
The precision mechanical workshop has the following available departments:
- Department of Design and Technology;
- Services for providing tools and design documentation;
- Machining: milling, turning, machining of special gears;
- Department of Electroerosion Machining;
- Assembly Area.
The Department of Special Gear Processing houses incision, grinding, testing and measuring machines of the American company GLEASON. Depending on the type of equipment and the dimensions Ø1200 mm; Ø800 mm; Ø600 mm; Ø400 mm; Ø125 / 100 mm (cylindrical), as well as Ø1000; Ø600; Ø275 (conical), gear processing and grinding operations can be carried out.
The Department of Erosion and Grinding houses electric erosion machines of the Japanese company MITSUBISHI, such as the "erosive" (maximum size 300x300x250 mm), "erosion boring" (maximum size 400x250x240 mm) and "erosive immersion" (maximum size 400x300x300 mm).
The milling area houses milling machines of the Japanese company MAZAK for processing equipment and parts. These machines allow performing milling operations on products of geometric dimensions 3750x10000 mm, H = 1750 mm, and weight 43 tons.
The shop of the plant for the production of semi-finished metal has working zones for cutting and bending. Here, special equipment was installed for performing the following various metalworking works:
- the ability to bend steel sheets up to 12 meters long and up to 20 mm thick at different angles without using special designs on modern CNC bending machines;
- modern CNC bending machines with steel sheets can be used to bend pipes of length 6000 mm, thickness 22 mm, diameter up to 5000 mm, pipe and conical parts of length up to 3000 mm, thickness up to 20 mm, pipes of length 4000 mm, thickness 80 mm, diameter more than 800 mm, pipes of length 4000 mm, thickness 100 mm, diameter more than 2000 mm;
- Semi-automatic lathe machines for cutting pipes and drilling, used in the oil and gas industry, for processing pipes of maximum diameter 533 mm, length 12000 mm;
- Fully functional and fully automatic lathe milling machines (CNC) for the precise machining of parts for both turning and milling on one machine;
- Fully automated control system (CNC) Fanuc, vertical, 3 axes of processing centers;
- Fully automated vertical lathe (CNC) for processing various types of cylindrical parts and body parts;
- Multifunctional fully automatic vertical lathe Fanuc (CNC);
- Semi-automatic horizontal and internal polishing CNC machine;
- Alignment machine for the manufacture of steel sheets of thickness 10 ÷ 60 mm, width 2500 mm.
The foundation of the press workshop, which was part of the machining plant, was laid on May 26, 2010 and commissioned into operation in September 2011. The shop has two production areas: electrical support preparation and stamping.
The enterprise is equipped with modern high-tech lines and universal press equipment. At the press plant, various proprietary hydraulic press lines can accurately process parts of high-voltage poles for the project. The hydraulic press, which has no analogues in our Republic, is an excellent tool for processing various chassis and machine parts in engineering.
Currently, the workshop uses corner machines, hydraulic shears, screw compressors, machines for processing tank bases, 50-1600 ton press tools, a radial grinding machine, a universal milling machine, a brewing machine, a 63-ton hydraulic press, guillotine hydraulic shears, as well as twisting and turning machines.
The crane area is used for the repair and production of cranes. Single, double-sided crane types are produced here. More than 80 different types of cranes have been produced in this area. The production process is carried out under the full control of the Technical Department and the Quality Control Department, and each load-lifting crane is transferred to the customer after testing. All metal structures and equipment used in crane production are certified, and fully comply with international requirements. The price of manufactured cranes is determined in accordance with technical parameters. Cranes are manufactured in accordance with the following technical parameters:
- Carrying capacity – 1 T - 200 T;
- Pass – 3 m up to 36 m;
- Control system – at a distance, from the cabin and cable;
- Crane trucks – single and double.